Some of the biggest industrial names in Liverpool city region are among 24 businesses agreeing to make a switch from fossil fuels to hydrogen as part of the huge HyNet project. Tony McDonough reports
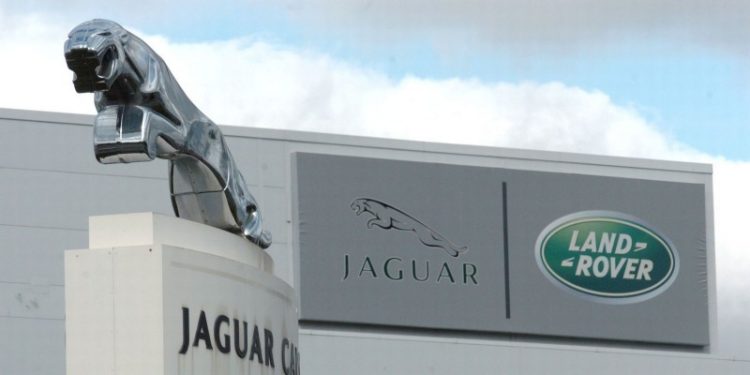
Some of the biggest companies in Liverpool city region are among 24 North West firms that are committing to switch from using fossil fuels to hydrogen.
Businesses including carmaker Jaguar Land Rover in Halewood, power generator InterGen at Rocksavage, consumer products giant Unilever in Wirral and glass giant Pilkington in St Helens, have all signed up to the North West-wide HyNet hydrogen scheme.
HyNet North West will initially build two hydrogen production plants at the Essar oil refinery in Ellesmere Port, on the banks of the Mersey, with more expected to follow. This will produce clean low carbon hydrogen from natural gas and pipe it to factories across the region.
Costing a combined £750m, the plants will separate the hydrogen from the carbon dioxide (CO2) during production. CO2 emissions are a major contributor to climate change so it will be captured and sent via pipeline to used up gas fields under Liverpool Bay for safe and permanent storage.
HyNet is a consortium of eight businesses led by clean energy specialist Progressive Energy. The consortium also includes ENI, Cadent, CF, INOVYN, Essar, Hanson and the University of Chester.
John Egan, HyNet hydrogen production project director at Progressive Energy, addressed business leaders at a forum organised by industry body Mersey Maritime in Birkenhead. He outlined how HyNet planned to slash the North West’s carbon emissions by 25% by 2030, equal to 10m tonnes a year, with the project becoming operational by 2025.
It has secured £72m to take the project forward and, along with another consortium on the East Coast, is one of the two first UK clusters out of six that has been given the go-ahead by the UK Government.
READ MORE: Essar submits plans for £750m hydrogen plants next to the Mersey
A demonstration of the use of hydrogen in an industrial manufacturing process has already been undertaken at Pilkington and a second at Unilever is planned in the coming months.
“We will make our industries sustainable and clean,” said Mr Egan. “Currently, the majority of industry emissions come from burning natural gas or other fossil fuels. Much of our industry, and power generation, can be switched relatively straightforwardly from natural gas to hydrogen. We call this fuel switching.”
He added there were some industries where it is not possible to avoid the release of CO2 by fuel switching, cement production being one example. He said HyNet would offer a second option for those companies whereby it will capture their carbon and send it for storage.
Hanson Cement near Mold in Flintshire is a leading member of the HyNet project so that it can decarbonise the production process this way.
“There is no single solution to the problem of carbon emissions so HyNet is bringing these two elements together,” explained Mr Egan. “As a country we could choose to eliminate our industrial emissions by just getting rid of our industries.
“But all that would do is move the emissions to other countries and lead to a loss of jobs and skills in the UK. HyNet will secure our industry in North West England and North East Wales and so grow the number of jobs in clean manufacturing.
“The scale of the project gives us a cost base that is affordable. If companies each tried to do this on their own it would be very expensive. Shared infrastructure is the key to the success of HyNet. We have signed memoranda of understanding with 24 major industrial businesses who want to start using hydrogen. The demand for what we are doing is now really strong.
Mr Egan also addressed concerns over the method HyNet will use to produce the hydrogen. There are three main methods of producing hydrogen and not all are equal when it comes to cutting carbon emissions.
Grey hydrogen is the least beneficial. Sometimes called “dirty hydrogen” it sees fossil fuels burned and the hydrogen extracted – but no attempt to capture the CO2 which is released into the atmosphere contributing to climate change.
Blue hydrogen, the method chosen by HyNet to start the project, also uses fossil fuels as the raw material – usually natural gas – but the CO2 is then captured and stored instead of being released.
Cleanest of all is green hydrogen. This is produced by separating the hydrogen in water molecules using a process called electrolysis and powered by renewable energy such as wind or solar.
In summer 2021 blue hydrogen was criticised in an academic report published by Cornell University in the US would lead to a significant escape of the captured CO2.
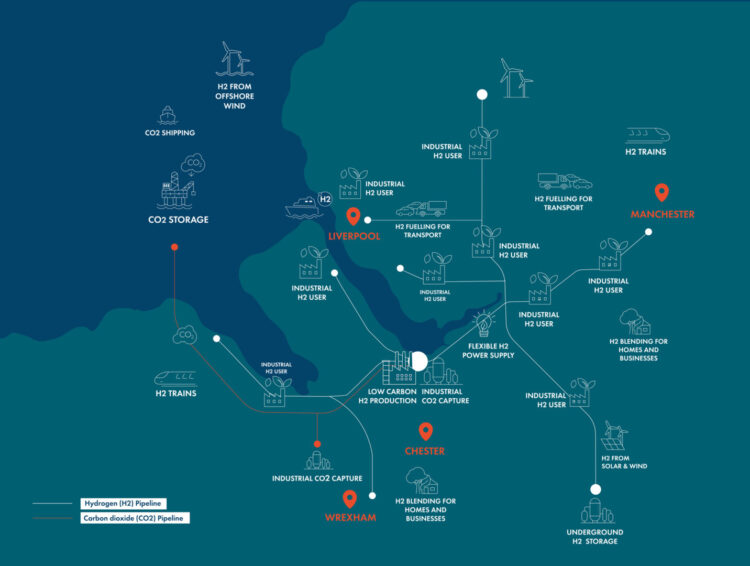
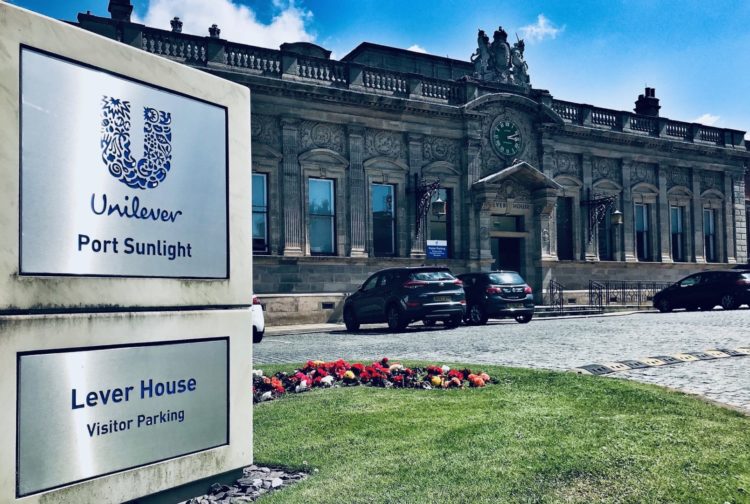
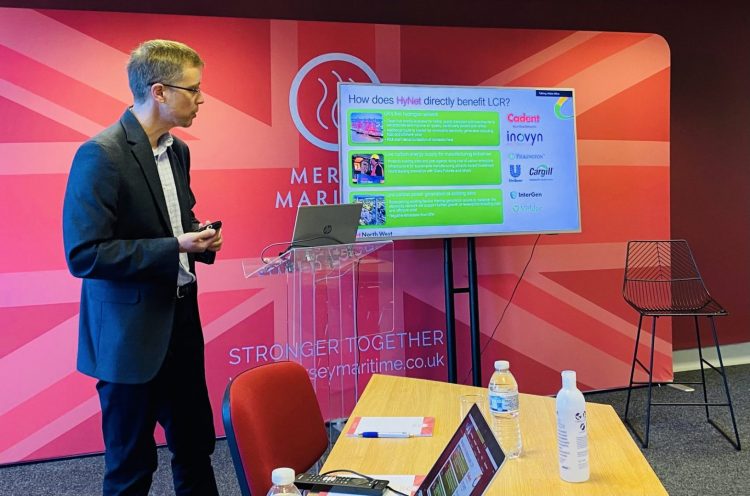
However, However, Mr Egan, consistent with the views of UK Government and the Committee on Climate Change, rejected this estimate and confirmed that the best in class process technology selected by HyNet, designed by UK company Johnson Matthey, will see the safe capture and storage of 97% of the CO2,
He added the Government would be setting a Low Carbon Hydrogen Standard that it would be obligated to meet to ensure that blue hydrogen provides a substantial reduction in emissions.
He also addressed why HyNet was initially focusing on blue hydrogen rather than going directly for green hydrogen. He said: “We need to move quickly to set up the network and infrastructure so we can start fuel switching in industry and other sectors across the entire region.
“Blue hydrogen has the scale and cost structure to enable that to happen quickly. Once the infrastructure is in place we expect to see increasing production of green hydrogen via electrolysis further down the line, benefitting from that infrastructure and increasing amounts of renewable power generation capacity.”
Over the next few years HyNet will install around 350km of pipeline around the North West which will supply the factories with hydrogen and transport the CO2 to be captured and stored. It is also utilising underground salt caverns in Cheshire to store the hydrogen in order to balance demand. Salt caverns are already used to store natural gas.
And Mr Egan says using hydrogen for industry is just the start. He explained: “Industry is going to create the anchor demand for hydrogen but it is also important we eventually look to power transport and homes – that is a critical part of the clean energy transformation.
“What we are looking to do here is really, really ambitious – but it is not pie in the sky, as demonstrated by Government selecting HyNet as one of the Track 1 clusters. This is absolutely achievable.”