JLR says £110m investment at Halewood will go ahead despite £1bn cutbacks
Britain’s biggest carmaker says it is committed to bringing the new Evoque model to Merseyside despite its battles with falling sales and profits. Tony McDonough reports
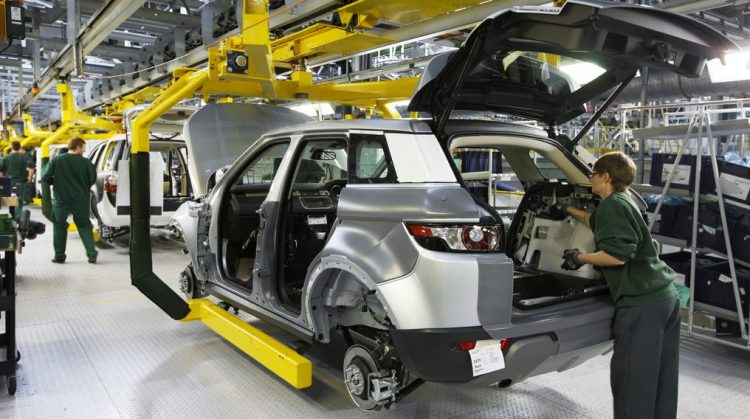
Carmaker Jaguar Land Rover (JLR) will proceed with the planned £110m investment into its Merseyside factory despite revealing it was going to slash costs in its UK operations by £1bn.
On Thursday JLR, which employs more than 4,000 people at Halewood assembling the Evoque and Discovery Sport models, reported a pre-tac loss of £90m in the three months to the end of September and a loss of £354m for the first half of its financial year.
Owned by India-based Tata Motors, JLR directly employs around 40,000 people in the UK and many more in the wider supply chain, making it the biggest auto maker in the country.
Falling sales
It said retail sales of its vehicles were down 13.2% year-on-year in the second quarter of 2018, with wholesale sales plummeting 14.7%. The company has faced significant headwinds in recent months with falling sales in its biggest market in China and a drop in diesel sales in the UK and Europe.
Around 90% of the vehicles it produces in the UK are diesel-powered and Governments are now cracking down on diesel with hefty tax rises and this is hitting sales. JLR is also anxious of the possible impact of a no-deal Brexit.
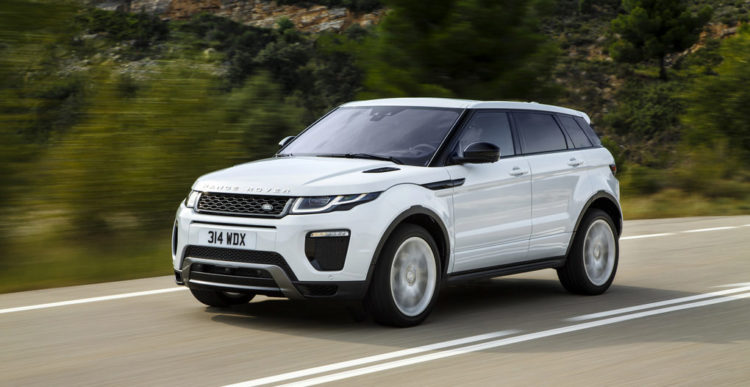
In June, the company announced the next generation Evoque model would be built on Merseyside, securing the future of its Halewood factory for a number of years to come. It said that investment would total £110m and has told LBN it will go ahead as planned.
However, prospects for JLR’s other plants Solihull, Castle Bromwich and Wolverhampton are less certain with the company yet to fully commit to a proposal to convert production in the West Midlands to electric vehicles.
Cost-cutting
In recent months JLR’s UK operations have been losing a million pounds a day and it has launched a £2.5bn turnaround plan involving cost-cutting and reductions in planned investment.
The firm has already cut 1,000 jobs in the West Midlands this year with an unscheduled shutdown this autumn of the Solihull plant and the Castle Bromwich factory going on a three-day week until Christmas.
Earlier this year chief executive Ralph Speth said it expected full-year profits for the year to March 2019 to come in at between £1bn and £1.75bn. It reported a profit of £1.5bn in 2017/18. However, he has now scaled back those ambitions with a target of breaking even.
He said: “We continue to see more challenging market conditions. Our results were undermined by slowing demand in China along with continued uncertainty in Europe over diesel, Brexit and the WLTP (new vehicle emissions testing regime) changeover.”