Liverpool-based experts on £180bn mission
Engineers at the Manufacturing Technology Centre in Liverpool say they are working on key projects that could help boost UK industry by £180bn. Tony McDonough reports

UK industry could benefit to the tune of £180bn (source: Made Smarter review) over the next decade if it accelerates its adoption of technologies such as robotics and automation.
That was the message delivered by Jim Brown, a senior research engineer at the Liverpool headquarters of the Manufacturing Technology Centre (MTC), to the Liverpool city region maritime sector.
Jim was addressing the March Mersey Maritime Face-2-Face monthly networking event, held at MTC’s base in Liverpool Science Park.
Dr Charlie Whitford, director of regional strategy and engagement at the MTC spoke first. He explained what the organisation is and its purpose. He said it was an industry-led non-profit research and technology organisation.
Working under the umbrella of the UK Government’s High Value Manufacturing Catapult, MTC employs around 1,000 people, the bulk of whom are engineers. Its Liverpool team, established in 2015, is now 100-strong.
“Essentially we are there to support industries to adopt technologies and adopt the right business models and adopt the right skills in order to be able to make the most of those technologies,” said Charlie.
“We look to understand the different journeys companies go on when adopting technologies. We also deliver apprenticeships. In Liverpool we are doing a Level 2 lean manufacturing apprenticeship and we are looking to expand that into Level 3 and 4.”
Jim has worked at the MTC for around 18 months. He joined from Wirral-based Survitec, a leading manufacturer in aerospace, defence and maritime. For 23 years he was with the Fleet Air Arm Branch of the Royal Navy, working aboard aircraft carriers and destroyers.
“In the past five years the MTC has delivered around 84 industrial projects for shipbuilding OEMs (original equipment manufacturers).
“Our core focus and challenges has been improving safety, increasing productivity, improving quality, skills shortages and sustainability.
“Sometimes there are very old methods of manufacturing. We try to introduce technologies into processes and improve efficiency. That is a challenge because we are dealing with old methods and old technologies that are trusted.
“It is about educating people how those new technologies will help. Also, it is working with an ageing workforce and bringing in new people. There is a need to transfer that knowledge from the old workforce to the new one.
“I have been on the shop floor and I understand that something valuable that is in someone’s head can stay in someone’s head. So it is about taking those people along on the journey, protecting the workforce and future-proofing the business.
“In terms of safety we know that technology can reduce risk. In essence we can remove the human element from hazardous processes. It is about getting the information from that end user and then showing them how it can be done more safely.”
Key to improving productivity, efficiency and safety is adopting technologies such as automation and robotics, Jim insisted. But he added there was often resistance. Two of the biggest worries people have is the upfront cost and the impact on jobs.
He explained: “There are challenges because there is resistance to change as well as finance implications. It can come with a cost but those costs can be recouped later on.
“It is also about combating the myth that it will take someone’s job. What we find is that adopting new technology frees people from mundane tasks and allows them to be upskilled to do something that is more valuable to the business.”
Jim is currently working on a major manufacturing project within the maritime sector. He says it offers a fascinating insight into one of the big challenges the sector faces – bringing in young people with the right skills to replace the ageing workforce.
“As part of this project we are looking at future skills. Having done some research, it is clear there needs to be a drive in maritime in bringing in new people and making it attractive for career paths.
“One of the challenges is getting the message out there about how skills can make careers in maritime more attractive. And it is that adoption of new technologies that will attract people into the industry.
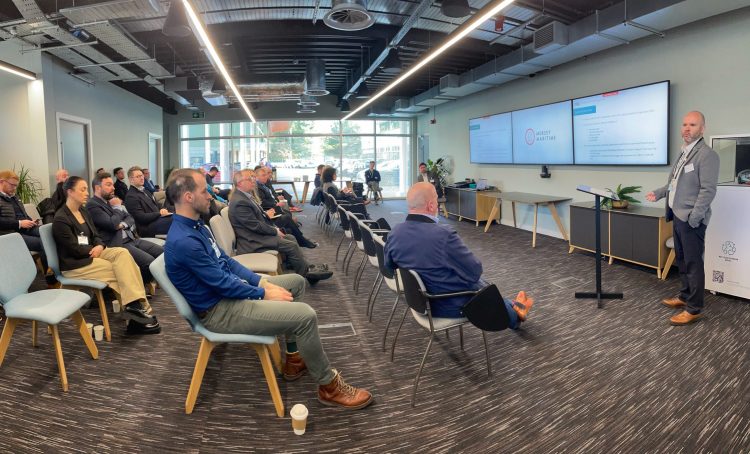
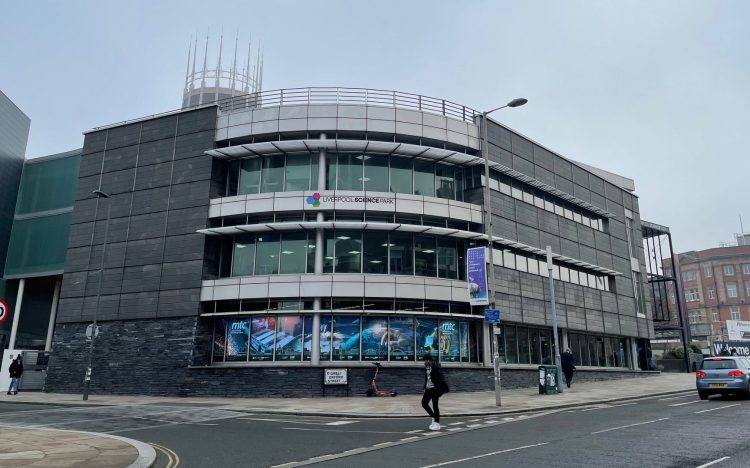
“On the programme I am working on at the moment we have been looking at the workforce. It is an ageing workforce using manufacturing processes that have not been optimised to keep up with changing technologies.
“They are now bringing in younger people, but the challenge is to bridge that gap. They need to take that old workforce on that journey and introduce the younger workers to the skills they will need.
“Within that we have to introduce new technology to ensure the job can get done. It is all very well introducing a new piece of kit but if the levels of understanding don’t fit then we have to identify the right skills and competencies.
“We have formed a future skills team. They have started to put together high-level job role profiles that will comprise competency statements to match the right people to the right processes.”
READ MORE: £6bn ‘barrage across the Mersey’ takes step forward
READ MORE: Rail link can help create 8,000 Sci-Tech Daresbury jobs
Another colleague of Jim’s is John Stretton, director of aerospace, defence and security, who addressed the event via video link. He said the key to attracting a new generation of people into the maritime sector was to emphasise the “stability and longevity” of careers in the industry.
“For the past few years there has been much more volatility in careers in many sectors, he explained. “The breadth of opportunities in the maritime sector means it can offer that stability.”
Jim concluded: “Maritime offers a multitude of roles. There are so many different opportunities on offer that will attract young people into the sector.”