Knowsley Lifts – from small beginnings to a UK leader
Co-director and co-founder of Knowsley Lifts, Stephen Fitzgerald, talks about the past, present and future of this fast-growing business…

What does the business do?
We are a multi-disciplinary business who’s roots began in Knowsley, with our HQ now in Edge Lane, Liverpool. Our business is separated into two distinct divisions: The service department which comprises a team of highly-skilled engineers that maintains and repairs lifts for clients across the UK; and the capital projects team which secures and delivers contracts for the design, installation and replacement of lifts.
What is the history of the company?
Leaving school in 1988, I landed an apprentice lift engineer position for the largest UK lift company, Express Lifts. After qualifying I was partnered alongside another engineer called Tommy Murphy, both individually working our way to regional technician positions during the early 1990s.
By the mid-1990s Tommy and I had discussed leaving and setting up our own business together. In 1997, the opportunity came along when Express Lifts was acquired by Otis, a multi-national company. Following the takeover we felt the clients were not getting the same level of service, so we decided to take the plunge and go it alone.
For the first three years we worked mainly as sub-contactors to larger companies but, in 2000, we felt we wanted to move away from that and start bidding for work ourselves. And so Knowsley Lifts was born as a limited company. Since then we have gone from strength to strength.
In 2002 we were accredited by LEIA, the Lift and Escalator Industry Association, the UK Lift Industry Governing Body, like the ABTA of the lift industry. 2007 was a real breakthrough year as we secured a £2.4m contract to replace 13 lifts, and install four new ones, at the Exchange Flags office complex in Liverpool.
In 2012 we surpassed the 1,000 lifts milestone and in 2014 we won what was a prestigious contract to install the lifts for the refurbished Everyman Theatre, which eventually won the RIBA Stirling Prize. In 2017 we were rated number one for sales growth among the 369 largest companies in the sector in the UK.
Who are the key people in Knowsley Lifts?
The quality of the people within our team and across all departments of our business is one of the things that sets us apart. They are a fantastic asset.
Myself and Tommy are the founders and the co-directors. Then we have Carey Oakes, who is our operations director. She predominantly looks after the major projects side of the business and plays a critical role in our ongoing growth.
Jay Maloney is our service director and he oversees the team of engineers who go out to maintain and repair lifts for our clients. In 2001 we took on our first apprentices and Jay was one of them.
Since then we have brought through 20 apprentices and many of them are still working for us. We have invested in them and they have repaid that faith by helping become the amazing business that we are today.
We currently employ around 30 people directly and there around another 40 engineers who we bring on as and when we need them. We have taken on one further new Capital Project Manager during this Covid period, with us looking to recruit further, seeing our headcount grow further in the very near future.
Give us a current snapshot of the business
As things stand we have a secured pipeline of work worth around £5m and that alone will keep us busy for the next 18 months. We have also tendered for a further £100m of work so, right now, we are extremely busy and with new capital projects landing on an almost weekly basis. It is clear we are going to continue this strong trend going forward.
We are not a manufacturer of lifts but we have a full in-house design team and we have a great relationship with the major global manufacturers and suppliers. Each job has its own specification and we have to supply a bespoke lift, depending on the job.
Much of our work is very niche and this is where, I believe, we outperform the bigger companies. They are more one-size-fits-all and often don’t offer the know-how and flexibility that we can. We can put a lift in any shaft and a lot of the work we do is not standard.
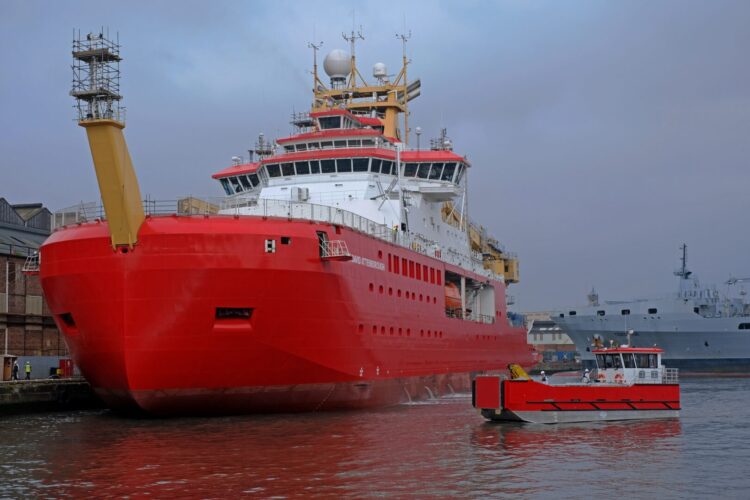
Our long-term clients list includes local authorities, NHS trusts (we are currently helping keeping the lifts going in the existing Royal Hospital in Liverpool), Mersey Tunnels, universities, the Ministry of Defence and (regional police forces) – so we are clearly doing something right. Our current capital projects include:
- Shakespeare North Playhouse, a 350-capacity theatre which is scheduled to open in Prescot in 2022. It is modelled on the ‘cockpit-in-court’ design popular in the Elizabethan era. We will be designing and installing three lifts. We had to go through a long selection process to get this job – it was a great result.
- Replacing one of the large lifts at St George’s Hall in Liverpool – a very high-spec job.
- A platform lift for Sefton Park Palm House – because of the tropical heat it was akin to installing a lift in jungle environments, with a very high level of specification and design required to successfully accomplish.
- And new lifts for the Rhyl Pavilion Theatre which helps us cement our reputation as a leading provider in North Wales.
There are also a number of legacy projects we are very proud of. We have installed lifts on the new £200m polar research vessel, RRS Sir David Attenborough which was built at Cammell Laird in Birkenhead.
We also installed a new service lift at the Royal Liver Building – (a very complex job which was shortlisted for the World Elevation Magazine Project of the Year in 2020), new lifts at Premier League football stadia and what is the highest platform lift in the UK at the Snowden visitor complex.
How has COVID-19 impacted your operations?
Early in the pandemic the start dates on some of our projects were put back, but the are backing up and running now. We had to furlough some of our engineers last year in tandem with the closure of clients sites and buildings but we have been back to full strength for about five months with the re-opening of buildings and sites allowing access to our teams to undertake our services.
How competitive is the market you operate in?
We have a growing reputation for being one of the best independents in the UK with the number of successful project bids we are awarded, and the number of customers who keep going back to us, is testament to that.